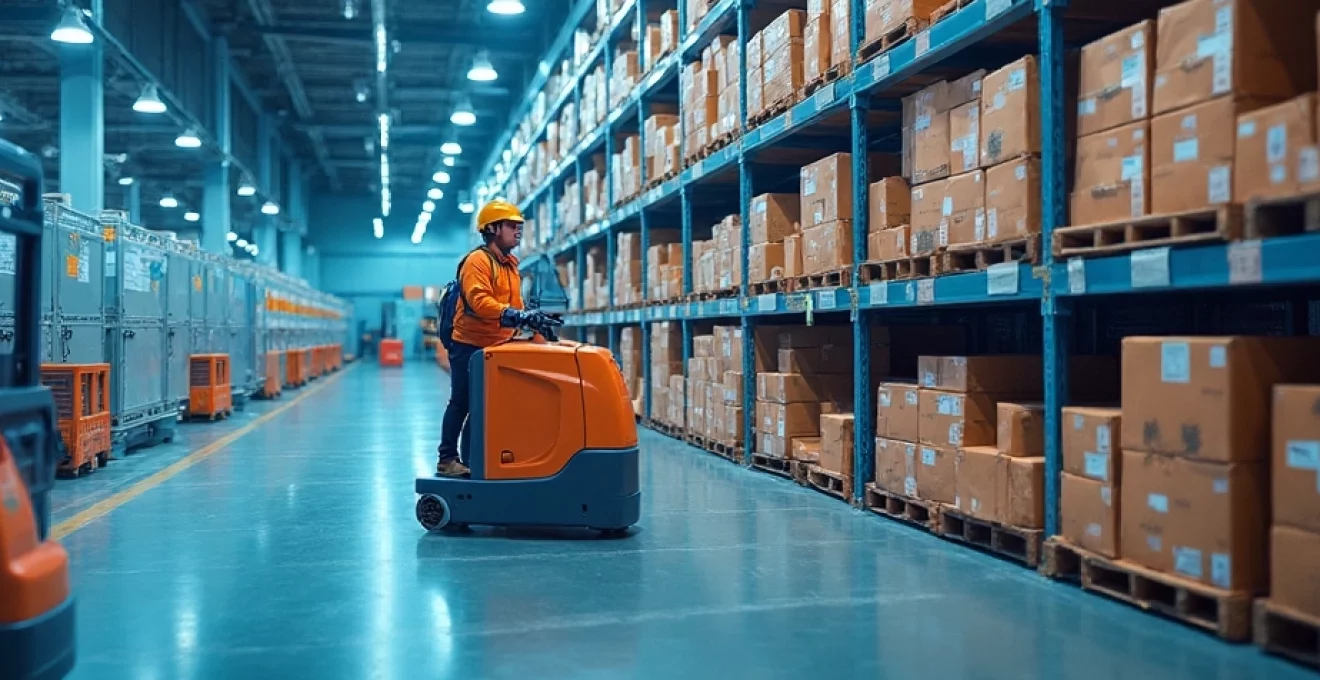
La optimización de la distribución en centros logísticos se ha convertido en un factor crítico para el éxito empresarial en la era del comercio electrónico y las entregas rápidas. Una disposición eficiente del espacio y los recursos no solo reduce costos operativos, sino que también mejora significativamente la productividad y la satisfacción del cliente. Al minimizar los desplazamientos innecesarios, las empresas pueden acelerar sus procesos, reducir errores y maximizar el rendimiento de su fuerza laboral. Esta estrategia se ha vuelto indispensable en un mercado donde la velocidad y la precisión son fundamentales para mantener la competitividad.
Análisis de flujos logísticos para reducción de desplazamientos
El primer paso hacia una distribución optimizada es realizar un análisis exhaustivo de los flujos logísticos existentes. Este proceso implica mapear detalladamente cada movimiento dentro del almacén, desde la recepción de mercancías hasta el despacho final. Al identificar patrones de movimiento y áreas de congestión, las empresas pueden rediseñar sus layouts para minimizar la distancia recorrida por los trabajadores y los productos.
Un análisis efectivo utiliza herramientas de simulación avanzadas que permiten visualizar el flujo de productos en tiempo real. Estas simulaciones ayudan a detectar cuellos de botella y ofrecen insights valiosos para la toma de decisiones. Por ejemplo, se puede determinar la ubicación óptima de los productos de alta rotación cerca de las zonas de picking, reduciendo así el tiempo de desplazamiento para los artículos más solicitados.
Además, el análisis de flujos logísticos debe considerar las variaciones estacionales y los picos de demanda. Un layout flexible que pueda adaptarse a estos cambios sin grandes modificaciones es esencial para mantener la eficiencia a lo largo del año. La implementación de zonas dinámicas que pueden expandirse o contraerse según la demanda es una estrategia cada vez más común en almacenes modernos.
Implementación de sistemas de gestión de almacenes (WMS)
La implementación de un sistema de gestión de almacenes (WMS) es fundamental para optimizar la distribución y reducir desplazamientos innecesarios. Un WMS robusto proporciona una visibilidad completa del inventario y las operaciones en tiempo real, permitiendo una toma de decisiones más informada y ágil.
Optimización de rutas con algoritmos de picking avanzados
Los algoritmos de picking avanzados son el corazón de un WMS eficiente. Estos sistemas utilizan inteligencia artificial y aprendizaje automático para calcular las rutas más eficientes para los operarios de almacén. Al optimizar las rutas de picking, se pueden reducir significativamente los desplazamientos, lo que se traduce en un aumento de la productividad y una disminución de los tiempos de preparación de pedidos.
Los algoritmos más sofisticados pueden incluso priorizar pedidos y agrupar tareas de manera inteligente, permitiendo que un solo operario complete múltiples pedidos en un solo recorrido. Esta estrategia de batch picking
puede reducir los desplazamientos hasta en un 50% en comparación con los métodos tradicionales de picking de pedidos individuales.
Integración de tecnología RFID para trazabilidad en tiempo real
La integración de tecnología RFID (Identificación por Radiofrecuencia) en el WMS lleva la trazabilidad y el control de inventario a un nuevo nivel. Los tags RFID permiten un seguimiento preciso y en tiempo real de cada producto dentro del almacén, eliminando la necesidad de escaneos manuales y reduciendo los errores humanos.
Con RFID, los operarios pueden localizar rápidamente los productos exactos que necesitan, evitando búsquedas innecesarias y desplazamientos improductivos. Además, esta tecnología facilita la implementación de sistemas de reposición automática, donde el WMS puede alertar cuando los niveles de stock están bajos y generar órdenes de reabastecimiento sin intervención humana.
Zonificación inteligente y slotting dinámico
La zonificación inteligente y el slotting dinámico son estrategias avanzadas que optimizan la ubicación de los productos dentro del almacén. El slotting dinámico utiliza datos históricos y previsiones de demanda para determinar la ubicación óptima de cada SKU, asegurando que los productos de alta rotación estén siempre en las posiciones más accesibles.
Esta estrategia no solo reduce los desplazamientos, sino que también mejora la ergonomía para los trabajadores al colocar los artículos más pesados o voluminosos en posiciones que minimizan el esfuerzo físico. Un sistema de slotting bien implementado puede mejorar la productividad del picking en hasta un 30% y reducir los tiempos de desplazamiento en un 40%.
La zonificación inteligente y el slotting dinámico son como un juego de ajedrez logístico, donde cada movimiento está calculado para maximizar la eficiencia y minimizar el esfuerzo.
Estrategias de cross-docking para agilizar la distribución
El cross-docking es una estrategia logística que minimiza el almacenamiento y acelera el flujo de productos a través del centro de distribución. En lugar de almacenar los productos recibidos, estos se transfieren directamente de los muelles de entrada a los de salida, reduciendo drásticamente los tiempos de manipulación y los desplazamientos innecesarios.
Sincronización de llegadas y salidas con software TMS
La implementación exitosa del cross-docking depende en gran medida de la sincronización precisa entre las llegadas de los proveedores y las salidas hacia los clientes. Los sistemas de gestión de transporte (TMS) juegan un papel crucial en esta coordinación, optimizando los horarios de carga y descarga para minimizar los tiempos de espera y maximizar la eficiencia del flujo de mercancías.
Un TMS avanzado puede integrar datos en tiempo real sobre el tráfico y las condiciones climáticas para ajustar dinámicamente los horarios de llegada y salida, asegurando un flujo constante de productos a través del centro de distribución. Esta sincronización precisa puede reducir los tiempos de permanencia de los productos en el almacén en hasta un 60%, disminuyendo significativamente la necesidad de manipulación y almacenamiento temporal.
Diseño de muelles y áreas de transferencia eficientes
El diseño de muelles y áreas de transferencia es crítico para el éxito de las operaciones de cross-docking. Un layout bien planificado facilita el movimiento fluido de mercancías y reduce la congestión en las áreas de carga y descarga. La implementación de muelles flexibles que pueden adaptarse a diferentes tipos de vehículos y cargas es una tendencia creciente en los centros de distribución modernos.
Además, la incorporación de tecnologías como dock scheduling systems
permite una asignación dinámica de muelles basada en el tipo de carga y la urgencia del envío. Estos sistemas pueden reducir los tiempos de espera en los muelles hasta en un 50% y mejorar la utilización del espacio en las áreas de transferencia.
Implementación de escaneo móvil y etiquetado automático
El escaneo móvil y el etiquetado automático son herramientas esenciales para agilizar las operaciones de cross-docking. Los dispositivos de escaneo móvil permiten a los operarios verificar y registrar los productos en movimiento, eliminando la necesidad de estaciones de trabajo fijas y reduciendo los desplazamientos innecesarios.
Por otro lado, los sistemas de etiquetado automático pueden generar y aplicar etiquetas de envío en tiempo real, basándose en la información recibida del WMS. Esta automatización no solo acelera el proceso de etiquetado, sino que también reduce los errores asociados con el etiquetado manual. La combinación de estas tecnologías puede aumentar la velocidad de procesamiento de cross-docking en hasta un 40%.
Automatización y robótica en centros de distribución
La automatización y la robótica están transformando radicalmente la eficiencia de los centros de distribución. Estas tecnologías no solo reducen la dependencia del trabajo manual, sino que también minimizan los desplazamientos innecesarios y optimizan el uso del espacio vertical.
Sistemas de clasificación automática (sorters) de alta velocidad
Los sistemas de clasificación automática, o sorters, son fundamentales para manejar grandes volúmenes de productos con precisión y rapidez. Estos sistemas pueden clasificar miles de artículos por hora, dirigiéndolos a las ubicaciones correctas dentro del almacén o directamente a las áreas de despacho para su envío.
Los sorters de última generación utilizan tecnología de visión artificial y deep learning para identificar y clasificar productos de forma instantánea, incluso aquellos con formas irregulares o embalajes no estándar. Esta capacidad de clasificación rápida y precisa puede reducir los tiempos de procesamiento en hasta un 70% y minimizar los errores de clasificación a menos del 0.1%.
Vehículos de guiado automático (AGV) para transporte interno
Los vehículos de guiado automático (AGV) están revolucionando el transporte interno en los centros de distribución. Estos robots autónomos pueden navegar de forma segura por el almacén, transportando productos entre diferentes zonas sin intervención humana. Los AGV más avanzados utilizan tecnología SLAM
(Simultaneous Localization and Mapping) para crear y actualizar mapas del entorno en tiempo real, adaptándose a cambios en el layout del almacén.
La implementación de AGV puede reducir los costos de mano de obra en hasta un 50% y aumentar la eficiencia del transporte interno en un 30%. Además, estos vehículos pueden operar 24/7, mejorando significativamente la utilización de los activos del almacén.
Tecnología de voice picking para operaciones hands-free
La tecnología de voice picking permite a los operarios trabajar con las manos libres, recibiendo instrucciones de picking a través de auriculares y confirmando las acciones mediante comandos de voz. Este enfoque no solo acelera el proceso de picking, sino que también reduce los errores al eliminar la necesidad de consultar listas de picking físicas o dispositivos manuales.
Los sistemas de voice picking pueden mejorar la productividad en hasta un 35% y reducir los errores de picking en más del 50%. Además, esta tecnología mejora la ergonomía y reduce la fatiga de los trabajadores, lo que se traduce en una mayor satisfacción laboral y menor rotación de personal.
La automatización y la robótica no solo optimizan los procesos, sino que también liberan el potencial humano para tareas de mayor valor añadido, creando un entorno de trabajo más eficiente y satisfactorio.
Análisis predictivo y big data en la planificación de rutas
El análisis predictivo y el big data están transformando la planificación de rutas en la logística moderna. Estas tecnologías permiten a las empresas anticipar demandas, optimizar recorridos y reducir significativamente los desplazamientos innecesarios tanto dentro como fuera del centro de distribución.
Modelos de machine learning para previsión de demanda
Los modelos de machine learning están revolucionando la forma en que las empresas prevén la demanda de productos. Estos algoritmos analizan grandes volúmenes de datos históricos, tendencias de mercado, eventos estacionales e incluso factores externos como el clima o eventos sociales para predecir con alta precisión los patrones de demanda futuros.
Una previsión de demanda precisa permite a los centros de distribución optimizar sus niveles de inventario y la disposición de los productos. Por ejemplo, se pueden posicionar estratégicamente los artículos que se espera tengan alta demanda en zonas de fácil acceso, reduciendo así los tiempos de picking y los desplazamientos. Los modelos de machine learning más avanzados pueden mejorar la precisión de las previsiones en hasta un 40% en comparación con los métodos tradicionales.
Optimización dinámica de rutas con datos de tráfico en tiempo real
La optimización dinámica de rutas utiliza datos de tráfico en tiempo real para ajustar continuamente los recorridos de los vehículos de reparto. Esta tecnología no solo considera la distancia entre puntos de entrega, sino también las condiciones actuales de tráfico, obras en carretera y otros factores que pueden afectar los tiempos de desplazamiento.
Los sistemas de optimización de rutas más avanzados pueden recalcular y ajustar las rutas en tiempo real, basándose en datos recibidos de GPS, sensores de tráfico y incluso redes sociales. Esta capacidad de adaptación dinámica puede reducir los tiempos de viaje en hasta un 15% y disminuir el consumo de combustible en un 20%, lo que se traduce en una reducción significativa de costos y emisiones de CO2.
Integración de variables meteorológicas en la planificación logística
La integración de datos meteorológicos en la planificación logística es una práctica cada vez más común en la industria. Las condiciones climáticas pueden tener un impacto significativo en los tiempos de entrega, la seguridad de los conductores y la integridad de ciertos productos sensibles a la temperatura.
Los sistemas de planificación avanzados utilizan APIs meteorológicas
para incorporar pronósticos precisos en sus algoritmos de optimización de rutas. Esto permite a las empresas anticipar y mitigar los efectos de condiciones climáticas adversas, ajustando las rutas o los horarios de entrega según sea necesario. La integración de variables meteorológicas puede mejorar la puntualidad de las entregas en hasta un 10% en condiciones climáticas difíciles.
Además, esta información es crucial para la gestión de productos sensibles a la temperatura. Los sistemas pueden recomendar rutas alternativas o ajustar los tiempos de salida para evitar exposiciones prolongadas a temperaturas extremas, reduciendo así el riesgo de daños a la mercancía y mejorando la calidad del servicio al cliente.
El uso combinado de estas tecnologías de análisis predictivo y big data no solo optimiza las rutas y reduce los desplazamientos innecesarios, sino que también mejora la eficiencia general de la cadena de suministro. Las empresas que adoptan estos enfoques avanzados están mejor posicionadas para enfrentar los desafíos logísticos del futuro, ofreciendo un servicio al cliente más eficiente y confiable.
La integración de estas tecnologías avanzadas de análisis y planificación está transformando la logística de última milla, permitiendo entregas más rápidas, eficientes y personalizadas. Las empresas que adoptan estos enfoques no solo reducen costos operativos, sino que también mejoran significativamente la experiencia del cliente, lo que se traduce en una mayor fidelización y ventaja competitiva en el mercado.
El big data y el análisis predictivo son los faros que guían la logística moderna hacia un futuro de eficiencia y precisión sin precedentes.
A medida que estas tecnologías continúan evolucionando, podemos esperar ver innovaciones aún más sorprendentes en la planificación de rutas y la optimización de la distribución. La clave para las empresas será mantenerse al día con estos avances y estar dispuestas a adaptar continuamente sus estrategias logísticas para aprovechar al máximo estas poderosas herramientas.