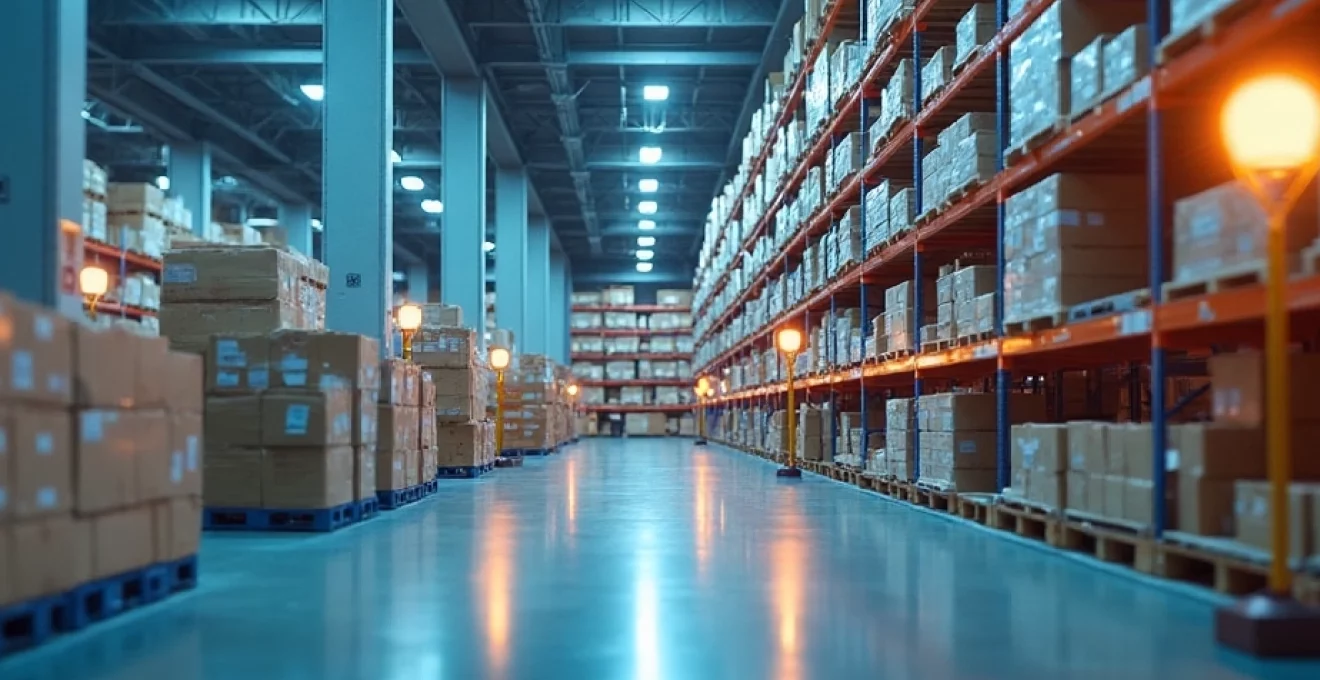
La gestión automatizada de almacenes se ha convertido en un pilar fundamental para las empresas que buscan optimizar sus operaciones logísticas y mejorar su competitividad en el mercado actual. Esta tecnología revolucionaria permite a las organizaciones aumentar la eficiencia, reducir costos y minimizar errores en sus procesos de almacenamiento y distribución. Al combinar software avanzado, hardware especializado y sistemas inteligentes, la automatización transforma radicalmente la forma en que se gestionan los inventarios y se procesan los pedidos.
En un mundo donde la rapidez y la precisión son cruciales, la gestión automatizada de almacenes ofrece una solución integral para hacer frente a los desafíos logísticos modernos. Desde la recepción de mercancías hasta el envío final, cada paso del proceso se optimiza para maximizar la productividad y minimizar los errores humanos. Esta evolución tecnológica no solo mejora la eficiencia operativa, sino que también proporciona una visibilidad sin precedentes sobre el inventario y el flujo de productos.
Fundamentos de la gestión automatizada de almacenes (WMS)
La gestión automatizada de almacenes se basa en un sistema de gestión de almacenes (WMS, por sus siglas en inglés) que actúa como el cerebro de toda la operación. Este software sofisticado coordina y optimiza todos los aspectos del almacenamiento, desde la ubicación de productos hasta la gestión de pedidos y el control de inventario. El WMS utiliza algoritmos avanzados para tomar decisiones en tiempo real, asegurando que cada movimiento dentro del almacén sea lo más eficiente posible.
Un componente clave de la gestión automatizada es la capacidad de integrar datos en tiempo real de múltiples fuentes. Esto incluye información sobre niveles de inventario, pedidos entrantes, capacidad de almacenamiento y rendimiento de los equipos. Al procesar y analizar estos datos continuamente, el sistema puede adaptar dinámicamente las estrategias de almacenamiento y picking para responder a las fluctuaciones de la demanda y optimizar el uso del espacio.
Además, la automatización permite implementar estrategias de almacenamiento más sofisticadas, como el almacenamiento caótico. En este enfoque, los productos se ubican en cualquier espacio disponible, en lugar de en ubicaciones fijas, lo que maximiza la utilización del espacio y reduce los tiempos de desplazamiento. El WMS mantiene un registro preciso de la ubicación de cada artículo, permitiendo una recuperación rápida y eficiente cuando sea necesario.
La gestión automatizada de almacenes no solo mejora la eficiencia operativa, sino que también proporciona una base sólida para la toma de decisiones estratégicas basadas en datos precisos y actualizados.
Tecnologías clave en la automatización de almacenes
La automatización de almacenes se apoya en una serie de tecnologías avanzadas que trabajan en conjunto para crear un ecosistema logístico altamente eficiente. Estas tecnologías no solo mejoran la precisión y la velocidad de las operaciones, sino que también proporcionan una visibilidad sin precedentes sobre todo el proceso de almacenamiento y distribución.
Sistemas de gestión de almacenes (WMS) como Manhattan associates
En el corazón de la automatización de almacenes se encuentran los sistemas de gestión de almacenes (WMS) como Manhattan Associates. Estos softwares especializados coordinan todas las actividades dentro del almacén, desde la recepción de mercancías hasta el envío de pedidos. Un WMS robusto como Manhattan Associates ofrece funcionalidades avanzadas que incluyen:
- Optimización de rutas de picking
- Gestión dinámica de ubicaciones
- Planificación de la carga de trabajo
- Análisis en tiempo real del rendimiento del almacén
- Integración con sistemas de automatización y robótica
La capacidad de estos sistemas para procesar grandes volúmenes de datos y tomar decisiones en tiempo real es fundamental para mantener la eficiencia en entornos logísticos complejos y de alta velocidad.
Identificación por radiofrecuencia (RFID) y códigos de barras
La tecnología RFID y los códigos de barras son esenciales para la trazabilidad precisa de los productos dentro del almacén. Los tags RFID permiten el seguimiento automático de los artículos sin necesidad de contacto visual directo, lo que acelera los procesos de recepción, inventario y envío. Por otro lado, los códigos de barras siguen siendo una solución rentable y ampliamente utilizada para la identificación de productos.
La combinación de estas tecnologías de identificación con el WMS permite un control de inventario en tiempo real, reduciendo drásticamente los errores y las discrepancias. Además, facilita la implementación de estrategias de almacenamiento avanzadas, como el almacenamiento caótico, donde los productos se ubican en cualquier espacio disponible para maximizar la eficiencia del almacén.
Vehículos guiados automatizados (AGV) y robots móviles autónomos (AMR)
Los AGVs y AMRs representan la vanguardia en la automatización del movimiento de materiales dentro del almacén. Estos robots inteligentes pueden navegar de forma autónoma por el almacén, transportando productos y realizando tareas de picking sin intervención humana directa. La diferencia clave entre ambos es que los AGVs siguen rutas predefinidas, mientras que los AMRs pueden calcular sus propias rutas y adaptarse dinámicamente a los cambios en el entorno del almacén.
El uso de estas tecnologías no solo aumenta la eficiencia y la precisión de las operaciones, sino que también mejora la seguridad al reducir el tráfico de carretillas elevadoras tradicionales. Además, estos sistemas pueden trabajar 24/7, lo que aumenta significativamente la productividad del almacén.
Sistemas de clasificación automática y cintas transportadoras inteligentes
Los sistemas de clasificación automática y las cintas transportadoras inteligentes son fundamentales para manejar grandes volúmenes de productos de manera eficiente. Estos sistemas pueden clasificar y dirigir automáticamente los productos a las áreas correctas del almacén, ya sea para almacenamiento o para la preparación de pedidos.
Las cintas transportadoras inteligentes están equipadas con sensores y sistemas de visión que pueden leer códigos de barras o etiquetas RFID en movimiento, permitiendo una clasificación precisa y en tiempo real de los productos. Esto es particularmente útil en operaciones de cross-docking, donde los productos deben ser rápidamente redirigidos de la recepción al envío sin pasar por el almacenamiento.
Integración con ERP y sistemas de gestión de la cadena de suministro
La verdadera potencia de la automatización de almacenes se realiza cuando se integra perfectamente con los sistemas ERP (Enterprise Resource Planning) y de gestión de la cadena de suministro de la empresa. Esta integración permite una visibilidad end-to-end de toda la cadena logística, desde la planificación de la demanda hasta la entrega final al cliente.
Al sincronizar datos en tiempo real entre estos sistemas, las empresas pueden optimizar sus niveles de inventario, mejorar la precisión de sus previsiones y responder rápidamente a los cambios en la demanda. Además, esta integración facilita la trazabilidad completa de los productos, lo cual es crucial para cumplir con requisitos regulatorios y gestionar eficazmente las devoluciones.
La integración de tecnologías avanzadas en la gestión de almacenes no solo mejora la eficiencia operativa, sino que también proporciona una base sólida para la transformación digital de toda la cadena de suministro.
Procesos optimizados mediante la gestión automatizada
La gestión automatizada de almacenes transforma radicalmente los procesos logísticos tradicionales, optimizando cada etapa desde la recepción hasta el envío. Esta optimización no solo aumenta la eficiencia y la precisión, sino que también proporciona una flexibilidad sin precedentes para adaptarse a las fluctuaciones de la demanda y los cambios en las estrategias de negocio.
Recepción y registro automático de mercancías
El proceso de recepción de mercancías se agiliza significativamente con la automatización. Los sistemas de escaneo automático pueden procesar rápidamente grandes volúmenes de productos entrantes, verificando la cantidad y la calidad contra las órdenes de compra. Las tecnologías RFID y los códigos de barras permiten un registro instantáneo en el sistema WMS, eliminando la necesidad de entrada manual de datos y reduciendo los errores asociados.
Una vez escaneados, los productos pueden ser automáticamente dirigidos a las áreas de almacenamiento apropiadas mediante sistemas de transporte automatizados como cintas transportadoras o AGVs. Esto no solo acelera el proceso de recepción, sino que también minimiza el tiempo que los productos pasan en las áreas de staging, mejorando el flujo general del almacén.
Almacenamiento dinámico y gestión de ubicaciones
La gestión automatizada permite implementar estrategias de almacenamiento dinámico que optimizan continuamente el uso del espacio del almacén. El WMS utiliza algoritmos avanzados para determinar la mejor ubicación para cada producto basándose en factores como la frecuencia de picking, el tamaño del producto, las características de almacenamiento requeridas y la disponibilidad de espacio.
Este enfoque dinámico permite una utilización más eficiente del espacio de almacenamiento y reduce los tiempos de desplazamiento durante el picking. Además, el sistema puede reorganizar automáticamente el inventario durante los períodos de baja actividad para optimizar aún más la disposición del almacén.
Picking optimizado con sistemas de voz y luz
Los sistemas de picking por voz y luz representan un salto significativo en la eficiencia y precisión de la preparación de pedidos. El picking por voz utiliza comandos de audio para guiar a los operarios a través del proceso de selección, permitiéndoles trabajar con las manos libres y los ojos enfocados en la tarea. Por otro lado, el picking por luz utiliza indicadores luminosos para señalar las ubicaciones exactas de los productos a seleccionar.
Estos sistemas, integrados con el WMS, pueden optimizar las rutas de picking para minimizar los desplazamientos y maximizar la eficiencia. Además, proporcionan una verificación en tiempo real de cada selección, reduciendo drásticamente los errores de picking.
Embalaje y etiquetado automatizado
La automatización del embalaje y etiquetado no solo acelera el proceso de preparación de pedidos, sino que también mejora la precisión y la personalización. Los sistemas automatizados pueden seleccionar el tamaño de caja óptimo para cada pedido, reduciendo los costos de envío y el uso de materiales de embalaje.
El etiquetado automático asegura que cada paquete tenga la información correcta y cumple con los requisitos de envío específicos del cliente o del transportista. Esto es particularmente importante en operaciones de e-commerce, donde la precisión en el etiquetado es crucial para evitar errores de envío y mejorar la satisfacción del cliente.
Gestión de inventario en tiempo real y reabastecimiento predictivo
La gestión automatizada proporciona una visibilidad en tiempo real del inventario, permitiendo un control más preciso de los niveles de stock. Los sistemas pueden monitorear continuamente los niveles de inventario y generar alertas automáticas cuando se necesita reabastecimiento.
Más allá del simple control de inventario, los sistemas avanzados utilizan análisis predictivo para anticipar las necesidades de reabastecimiento basándose en patrones históricos, tendencias de ventas y factores externos como la estacionalidad. Esto permite a las empresas mantener niveles óptimos de inventario, reduciendo tanto los excesos de stock como las roturas de stock.
Implementación de un sistema de gestión automatizada de almacenes
La implementación de un sistema de gestión automatizada de almacenes es un proceso complejo que requiere una planificación cuidadosa y una ejecución meticulosa. Este proceso no solo implica la instalación de nuevo software y hardware, sino también una transformación significativa en los procesos y la cultura organizacional.
Análisis de requisitos y selección de software WMS
El primer paso crucial en la implementación es realizar un análisis exhaustivo de los requisitos específicos del negocio. Esto implica evaluar los procesos actuales, identificar cuellos de botella y áreas de mejora, y definir claramente los objetivos de la automatización. Basándose en este análisis, se puede seleccionar el software WMS más adecuado que se ajuste a las necesidades específicas de la empresa.
La elección del WMS debe considerar factores como la escalabilidad, la compatibilidad con los sistemas existentes, la facilidad de uso y la capacidad de personalización. Es fundamental involucrar a todas las partes interesadas en este proceso de selección para asegurar que el sistema elegido satisfaga las necesidades de todos los departamentos afectados.
Diseño de layout y flujos de trabajo automatizados
Una vez seleccionado el WMS, el siguiente paso es diseñar o rediseñar el layout del almacén para optimizar los flujos de trabajo automatizados. Esto puede implicar cambios significativos en la disposición física del almacén, como la creación de nuevas zonas de picking, la instalación de sistemas de transportadores o la reorganización de las áreas de almacenamiento.
El diseño debe considerar la ergonomía y la eficiencia del movimiento, asegurando que los flujos de trabajo automatizados se integren de manera fluida con las operaciones manuales que aún puedan ser necesarias. Es crucial simular y probar estos nuevos flujos de trabajo antes de la implementación completa para identificar y resolver cualquier problema potencial.
Integración de hardware y sistemas de automatización
La integración del hardware de automatización, como AGVs, sistemas de clasificación automática y tecnologías RFID, es un paso crítico en la implementación. Esto requiere una coordinación cuidadosa entre los proveedores de hardware, los integradores de sistemas y el equipo interno de TI para asegurar una integración sin problemas con el WMS y otros sistemas existentes.
Es esencial establecer protocolos de comunicación claros entre los diferentes sistemas y realizar pruebas exhaustivas para garantizar que todos los componentes
funcionan de manera integrada y fluida. Durante esta fase, es crucial realizar pruebas de estrés para identificar y resolver cualquier cuello de botella o punto de fallo potencial en el sistema automatizado.
Capacitación del personal y gestión del cambio
La implementación exitosa de un sistema de gestión automatizada de almacenes no solo depende de la tecnología, sino también de las personas que la utilizarán. La capacitación exhaustiva del personal es fundamental para garantizar que todos los empleados comprendan cómo operar el nuevo sistema y aprovechar al máximo sus capacidades.
Además de la formación técnica, es crucial gestionar el cambio organizacional que conlleva la automatización. Esto implica comunicar claramente los beneficios del nuevo sistema, abordar las preocupaciones de los empleados y fomentar una cultura de mejora continua. La participación activa de los empleados en el proceso de implementación puede ayudar a generar aceptación y entusiasmo por el nuevo sistema.
Métricas y KPIs para evaluar la eficiencia de la automatización
Para garantizar que la inversión en automatización esté generando los resultados esperados, es esencial establecer y monitorear regularmente un conjunto de métricas y KPIs (Indicadores Clave de Rendimiento). Estas medidas proporcionan una visión objetiva del rendimiento del sistema y ayudan a identificar áreas de mejora continua.
Algunas de las métricas más importantes para evaluar la eficiencia de un almacén automatizado incluyen:
- Precisión del inventario: Mide la exactitud entre el inventario físico y los registros del sistema.
- Tiempo de ciclo del pedido: El tiempo total desde que se recibe un pedido hasta que se envía.
- Productividad del picking: Número de líneas o unidades recogidas por hora/empleado.
- Utilización del espacio: Porcentaje del espacio de almacenamiento utilizado eficientemente.
- Tasa de error en los envíos: Porcentaje de pedidos enviados con errores.
Es importante establecer benchmarks para estas métricas basados en los estándares de la industria y los objetivos específicos de la empresa. El seguimiento regular de estos KPIs permite a las organizaciones identificar tendencias, celebrar éxitos y abordar rápidamente cualquier problema de rendimiento.
Tendencias futuras en la gestión automatizada de almacenes
El campo de la gestión automatizada de almacenes está en constante evolución, impulsado por avances tecnológicos y cambios en las demandas del mercado. Comprender estas tendencias emergentes es crucial para que las empresas se mantengan competitivas y preparen sus operaciones logísticas para el futuro.
Inteligencia artificial y machine learning en la optimización de almacenes
La inteligencia artificial (IA) y el machine learning están transformando la forma en que se gestionan los almacenes automatizados. Estos sistemas pueden analizar vastas cantidades de datos para identificar patrones y hacer predicciones precisas sobre la demanda, optimizar rutas de picking y mejorar la gestión del inventario.
Por ejemplo, los algoritmos de aprendizaje profundo pueden predecir con precisión cuándo un equipo necesitará mantenimiento, permitiendo un enfoque proactivo que minimiza el tiempo de inactividad. Además, la IA puede optimizar dinámicamente la disposición del almacén basándose en patrones de demanda en tiempo real, mejorando continuamente la eficiencia operativa.
Internet de las cosas (IoT) y sensores avanzados en la gestión de inventario
El Internet de las Cosas (IoT) está llevando la gestión de inventario a un nuevo nivel de precisión y eficiencia. Los sensores avanzados pueden monitorear en tiempo real no solo la ubicación de los productos, sino también su condición, temperatura y otros factores críticos. Esto es particularmente valioso para industrias como la farmacéutica o la alimentaria, donde el control de la cadena de frío es crucial.
La implementación de gemelos digitales del almacén, réplicas virtuales exactas del espacio físico, permite simular y optimizar procesos antes de implementarlos en el mundo real. Esta tecnología, combinada con datos en tiempo real de sensores IoT, ofrece una visibilidad sin precedentes sobre las operaciones del almacén.
Realidad aumentada y wearables para operaciones de almacén
La realidad aumentada (RA) y los dispositivos wearables están emergiendo como herramientas poderosas para mejorar la eficiencia y precisión de las operaciones manuales en el almacén. Los sistemas de picking asistidos por RA pueden guiar visualmente a los trabajadores a la ubicación exacta de los productos, superponiendo información digital sobre el entorno físico.
Los wearables, como gafas inteligentes o dispositivos de muñeca, pueden proporcionar información crítica a los trabajadores sin necesidad de que desvíen su atención de la tarea en cuestión. Esto no solo mejora la eficiencia, sino que también reduce los errores y mejora la seguridad laboral.
La integración de estas tecnologías emergentes en los sistemas de gestión automatizada de almacenes promete llevar la eficiencia logística a nuevos niveles, permitiendo operaciones más ágiles, precisas y adaptables a las cambiantes demandas del mercado.